Temporal segregation, a dynamic procedure to manage raw material quality variation in feed mills
PART.3
By Marcos Fraiha - Nutritionist, Doctor in Agriculture Engineering, Doctor of Veterinary Medicine.
In a series of articles, I promised you to answer a simple question:
What is the return on investment of feed ingredient analysis for a feed mill operation?
In the first discussion, we estimated the cost impact of raw material natural variability. Do you remember that? I indicated the financial impact of corn quality variation for a feed mill. For example, I took the following situation: corn price at EURO 250/MT, volume consumed per year at 100 000 MT, and standard quality variation at 1,6. In this case, the total budget expenditure in corn would be EURO 25 million (corn price x volume), and the financial impact of natural variation would represent EURO 695 000.
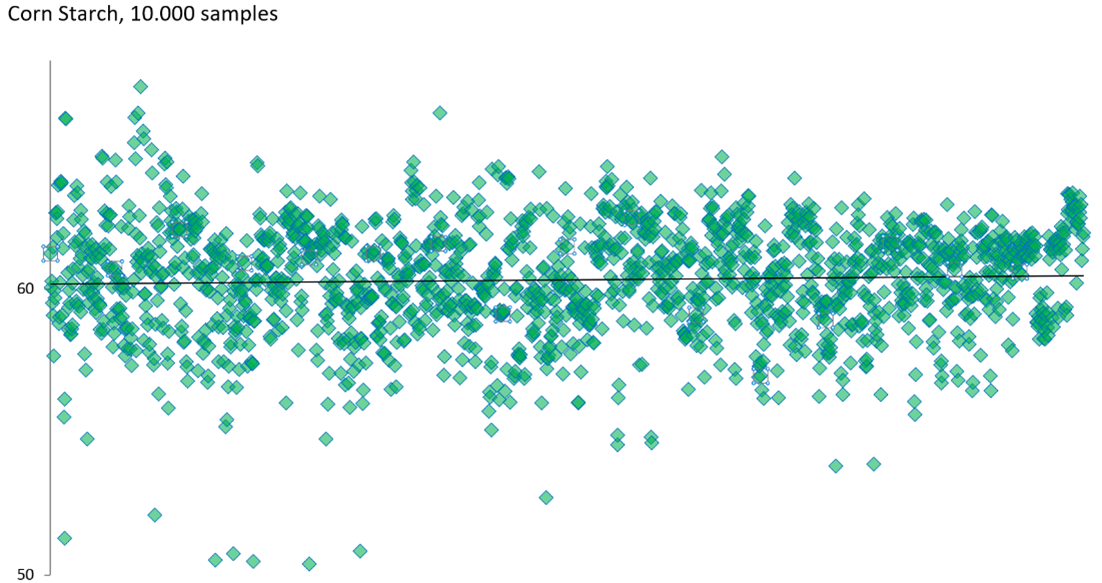
Ingredient identity preservation optimizes nutrient variability usage and cost savings but requires extra space and investments in silos. We propose time segregation as an alternative.
Feed formulators struggle with natural nutrient variations in ingredients, which can lead to variable final product specs or out-of-spec products. To prevent this, companies analyze every batch of ingredients.
Figure 1 shows starch variability in corn batches. Formulators must constantly adjust recipes based on lab analysis. The standard procedure recommends physical segregation, but many professionals struggle with implementation as it requires extra silos and constant re-formulation.
The proper solution considers the entire feed production system, including ingredient flow and mixing. The red line in Figure 2 represents the correct solution. However, it demands a proper understanding of the quality change as the flow of ingredients passes through production.
As ingredient mixing occurs during silo loading/unloading and grinding, resulting in a different quality profile than individual cargo analysis, formulators must understand the quality identity change that occurs in a feed mill. This is unique to each feed mill and depends on the plant configuration, which is relatively easy to measure.
The mathematical estimation of nutritional parameters helps monitor quality and determine formula change timing based on the plant configuration. Two methods exist, depending on the sampling location, and their choice depends on how samples are collected and the laboratory's analysis procedures. For NIR systems, this becomes easy to process. Finally, the operational silo capacity and feed mill output will define formula revision frequency. Depending on the historical raw material variability, optimal financial impact typically requires 2-3 weeks between formula revisions.

Figure 3. Typical financial analysis of potential savings for feed mills using the Time Segregation concept.
When applied to the formulation routine, this technique can yield tens of millions of dollars in financial savings for a feed mill operation. This can be estimated in advance using the Trouw Nutrition MyNutriOpt portal and the Roboto NIR Value calculator (Figures 3 and 4).
Figure 4. Example of recommendation on raw material Time Segregation limits for formula changes.
If you want to follow up with deeper discussions, please get in touch with your Trouw Nutrition contact, and we can organize an exclusive call.