Temporal segregation, a dynamic procedure to manage raw material quality variation in feed mills
PART.2
By Marcos Fraiha - Marketing Director MEA Export
In a series of articles, I promised you to answer a simple question:
What is the return on investment of feed ingredient analysis for a feed mill operation?
To answer this question, you must combine different expertise. These include knowledge of raw material physicochemical properties and their variation, how animals digest raw materials, and how they are handled in a feed mill operation. Such knowledge can be transformed into actions by the formulation and quality departments. It depends on theoretical knowledge, but it can become practical actions that nutritionists and feed mill managers can implement in their operations. These actions can produce cost savings and competitiveness in animal and feed mill operations. These articles are organized in the following order and will appear exclusively in FeedMag.
- The last article discussed “Value of lab analysis in feed production and why quantity matters.”
- This article will focus on “Raw material quality natural variation and its impact on formula cost and animal performance.”
- The next FeedMag article will discuss “Temporal quality segregation method, silo-free quality segregation for financial impact.”
In the last discussion, we estimated the cost impact of raw material natural variability. Do you remember that? I indicated the financial impact of corn quality variation for a feed mill. For example, I took the following situation: corn price at EURO 250/MT, volume consumed per year at 100 000 MT, and standard quality variation at 1,6. In this case, the total budget expenditure in corn would be EURO 25 million (corn price x volume), and the financial impact of natural variation would represent EURO 695 000.
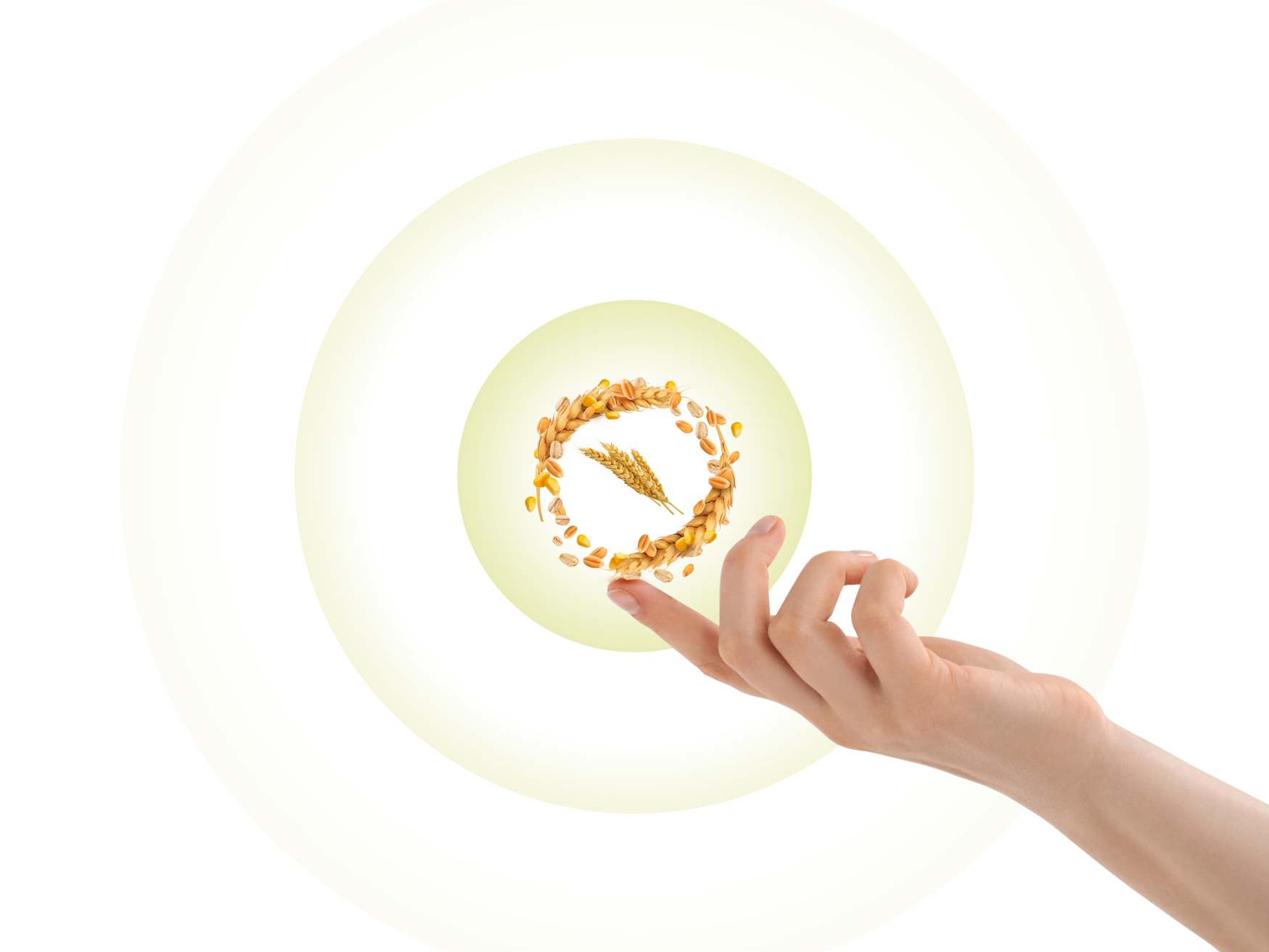
In the present text, I will explain further how this calculation is done and how we transform nutrient variation into financial measurement. This understanding will enable you to grasp why a lab has value to a feed mill operation and how we can measure its return on investment. Above all, you will be able to understand why it's so important to have as many sample analyses as possible to guide decisions on formula changes as ingredient quality varies.
For those of you experienced in animal raising production, you know very well that good animal performance means good financial performance. If animals do not grow or produce less milk, fewer eggs, or fewer offspring, you are paying for their maintenance with less output. This is very clear and intuitive, and it’s relatively easy to calculate profit or loss due to a lousy feed due to high raw material nutritional variation. Too much or too little energy, or too much or too little amino acids, the animals waste it because of an energy-nitrogen imbalance.
What is not so obvious is the rationale for evaluating the financial impact of raw material nutrient variation on the feed itself.
Before we explain it further, let’s define things clearly. What do I mean by nutrient variation? Suppose you acquired corn, or soybean meal. Nutritionists do not say, “Corn is corn.” They always ask: “Corn? What starch and protein level?” Or they ask: “What soybean meal? The real one, hexane extracted? What protein and solubility level?” This way, you can have corn 8% or 7,5% protein, or corn 60% or 65% starch. Similarly, you may have soybean meal 48%, 75% solubility, or soybean meal 48%, 82% solubility.
The opportunity is here: Contractually, you pay the same market-defined prices for these ingredients. These ingredients are used to produce formulas according to precise client specifications, legislation guidelines, or commercial promises. You give nutrient stocks away for free if you produce end products beyond specs. On the other hand, if ingredients come with lower specs than the formula you designed, you will need to correct the difference by increasing its quantity or by including another richer ingredient to compensate. In both cases, these deviations have consequences for your cost management.
Once I had a debate with a senior, very experienced nutritionist. He said this: “There is no financial problem in raw material quality variation. Since the variation follows a normal distribution, some cargo of ingredient A will have fewer nutrients, and some cargo will have more nutrients than average. In a few months, you will regain what you lost before”. He is right on one point and wrong on another. Yes, the variation is cyclical, and nutrients go up and down constantly. However, this cycle takes several weeks or months to complete. Based on historical statistics, you will regain what you lost before, but only in terms of stock accounting, not financial accounting. But here is where he was wrong: most feed mills set a price for their products very regularly, based on raw material prices of the moment.
I suggest now that you stop for a minute and think. What the wise nutritionist was proposing above is something like gambling. I rewrite his statement above to fit the analogy of playing with money: Quality variations of ingredients come and go. Today, I lose, but tomorrow, I win. It’s cyclical, and the ups and downs have the same amplitude. So, in the long run, I don’t lose anything. This indeed seems inconsequential if you don’t think of cash flows. Let’s analyze it seriously. Think of your feed mill operation and define how many thousand metric tons of feed you produce annually. Now, calculate how much corn and soybean meal you will purchase during this period. Now multiply it by the price you would pay today for these ingredients. What is the number you get when you sum them up? Now, think about the payment terms you have negotiated with your supplier. Do you know how often the cyclical up and down of ingredient variation runs in your factory? When should formulas be changed to avoid this trap? How can you stop gambling with the sum of money you just calculated?
In Trouw Nutrition, we built a model to define appropriate answers for these questions. We can define the natural variability of the most impactful ingredients and estimate the financial cost of doing nothing to correct it. Most importantly, we devised a method to indicate when and how to correct for such variability and the financial benefits of doing so.
To create such a model, we analyzed more than 100,000 samples worldwide based on diverse raw materials we received at Masterlab. To simplify this text, let's focus on corn only. As the significant nutritional contribution of corn is energy, and most of the energy from corn is stored as starch, we took it as the reference specification to evaluate its natural variation. The expected worldwide variation of starch in corn is 1,6 standard deviations from a 63% starch average corn. -"I don't get it!" - you may say. Let's translate: The statistics of all these worldwide samples indicated that corn starch content varied from 59 to 69%. This is a massive difference in energy content from different samples we had access. From the lowest starch-containing corn to the highest, there was a 10% difference. This means that 1 MT of corn could vary by up to 100 kg of starch content. This is the equivalent of having a formula requiring 60% of corn, but only 54% was added. Next, we connected this variation to the price of corn at a given moment and ran several simulations using multiblend formulation techniques for all animal species. The shadow value of starch was derived, and a financial value index for the variation unit was created. We can now estimate the financial impact of any feed mill anywhere by inputting some basic information on production, local costs, and ingredient variability data. The model can also recommend when to change formulas and how to segregate ingredients to optimize your nutrient stock control. Yes, you read well. I refer to nutrient stock instead of ingredient. It’s not a mistake. Our current NutriOpt tools allow us to manage ingredient stocks at the level of their nutrients. That’s a further expansion of precision nutrition.
I hear your thoughts. You read above about segregation. Ingredient identity preservation in feed milling is a well-known technique for optimizing nutrient variability usage and cost savings. But it demands extra space, extra silo, maybe investments, and so on. Right? That’s what we want to address in our third article coming up. We propose to finally explain the title of this series of articles: time segregation. I will show you how we can preserve quality identity without physical segregation.